The Production Line
May 11, 2022
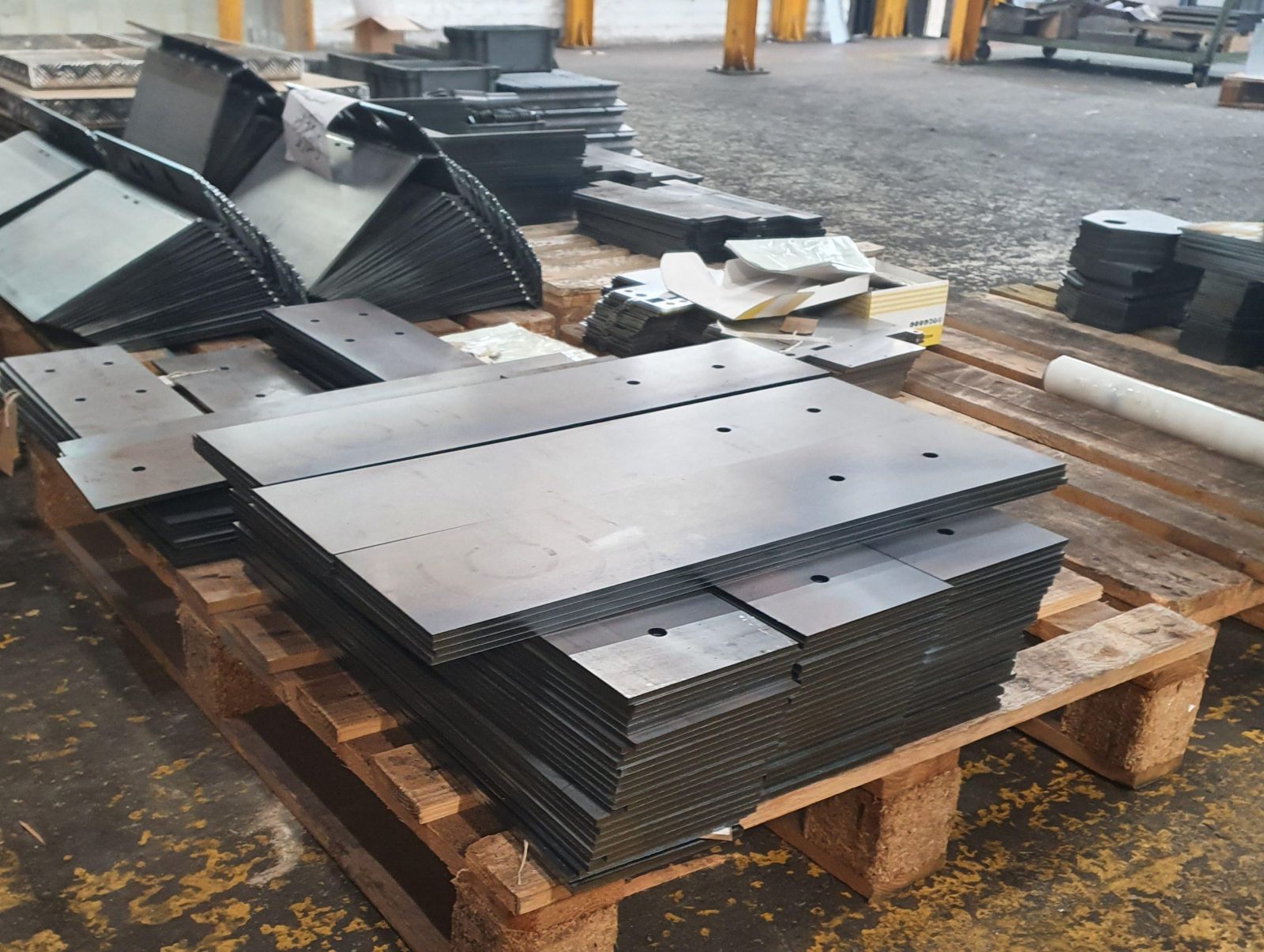
Robust steel foundations for quality street benches
These flat mild steel sheets have been laser cut for an innovative street furniture project. They will undergo bending, welding and dressing.
Each leg is made in two pieces. We bend the steel into a box-like profile, creating an effective and robust leg. We also manufacture the steel platforms which bolt on top of the legs and form a base ready for the custom-made timber slats.
May 11, 2022
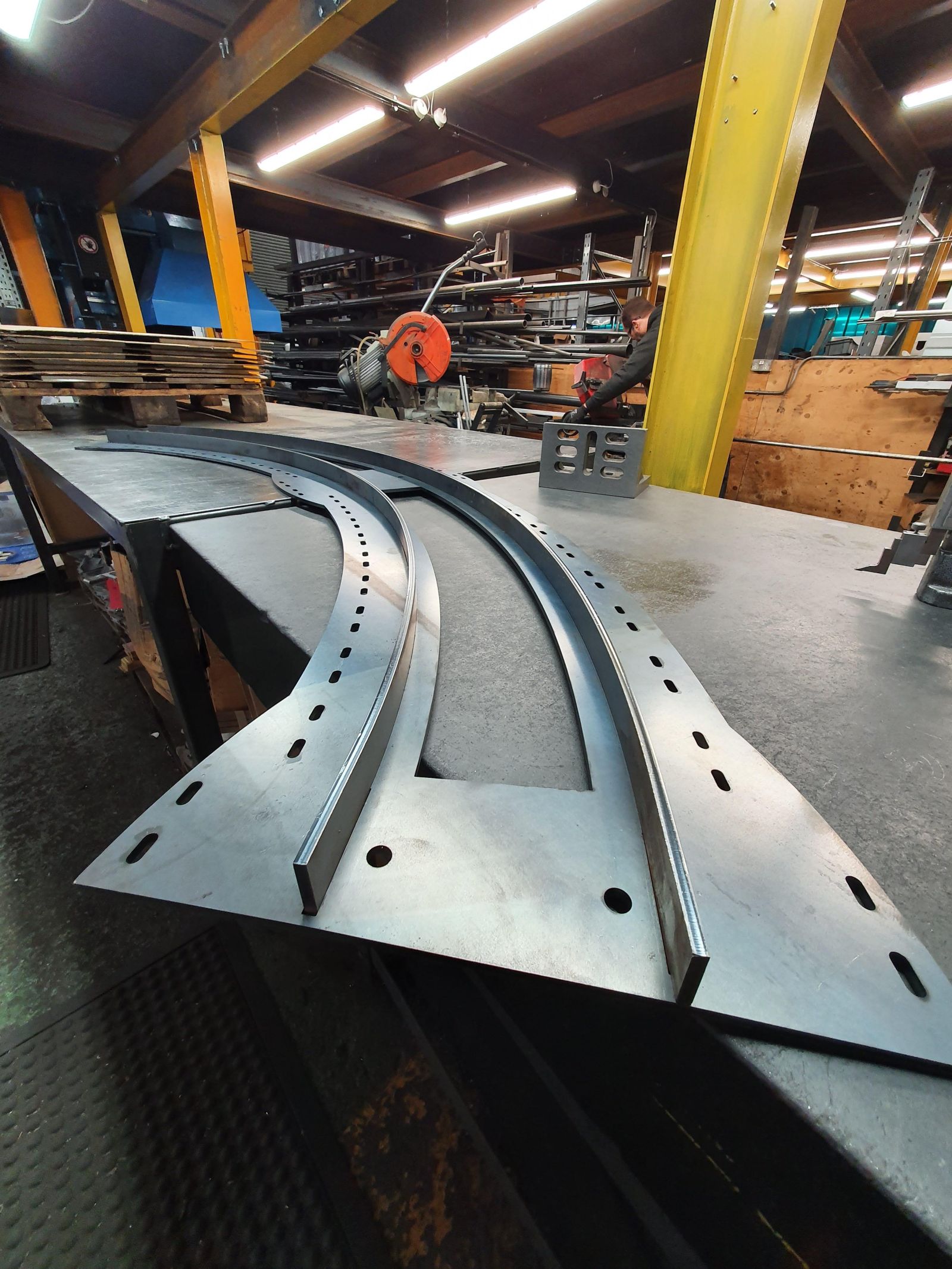
Laser cutting and fabrication for contemporary street furniture
Pictured is a recently manufactured steel platform that has been laser cut, rolled and assembled, prior to welding for a street furniture design company.
Bespoke iroko hardwood bench slats will fit on top of the platforms creating a high-end aesthetic. This steel and timber street bench has been manufactured as part of a town centre regeneration project. Our customer offers bespoke designs so our flexibility has proven to be key to the relationship.
Apr 29, 2022
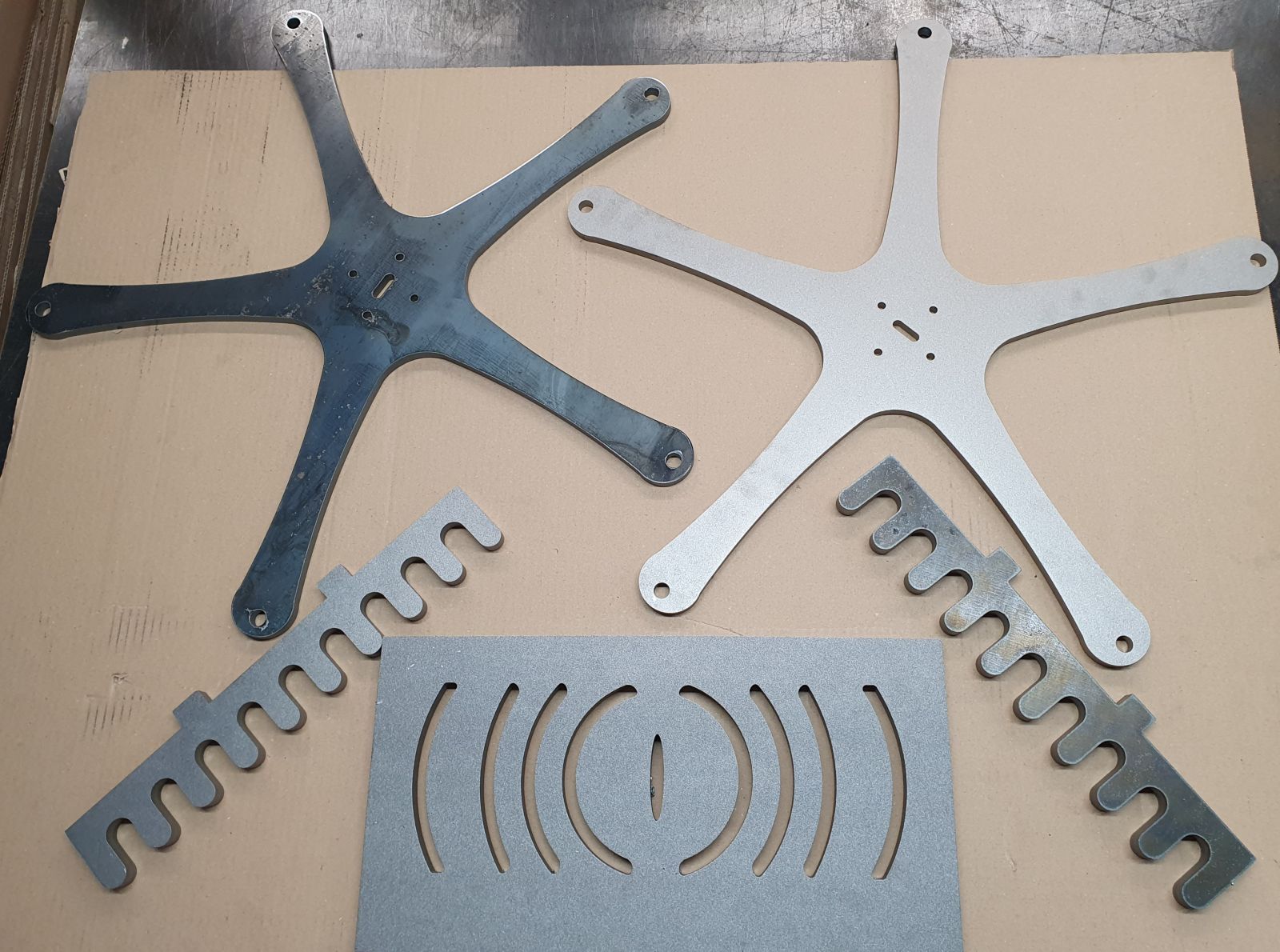
We now offer a shotblasting service
We have a Wheelabrator Smart Line Rotary Table Shot Blaster. Here you can see the fantastic job it does of cleaning and descaling metal, removing corrosion, rust and making parts look brand new.
It's used in preparation for surface treatment and powder coating. We use high-quality steel shot to ensure an excellent quality finish - to which our powder coating bonds seamlessly.
Jan 31, 2022
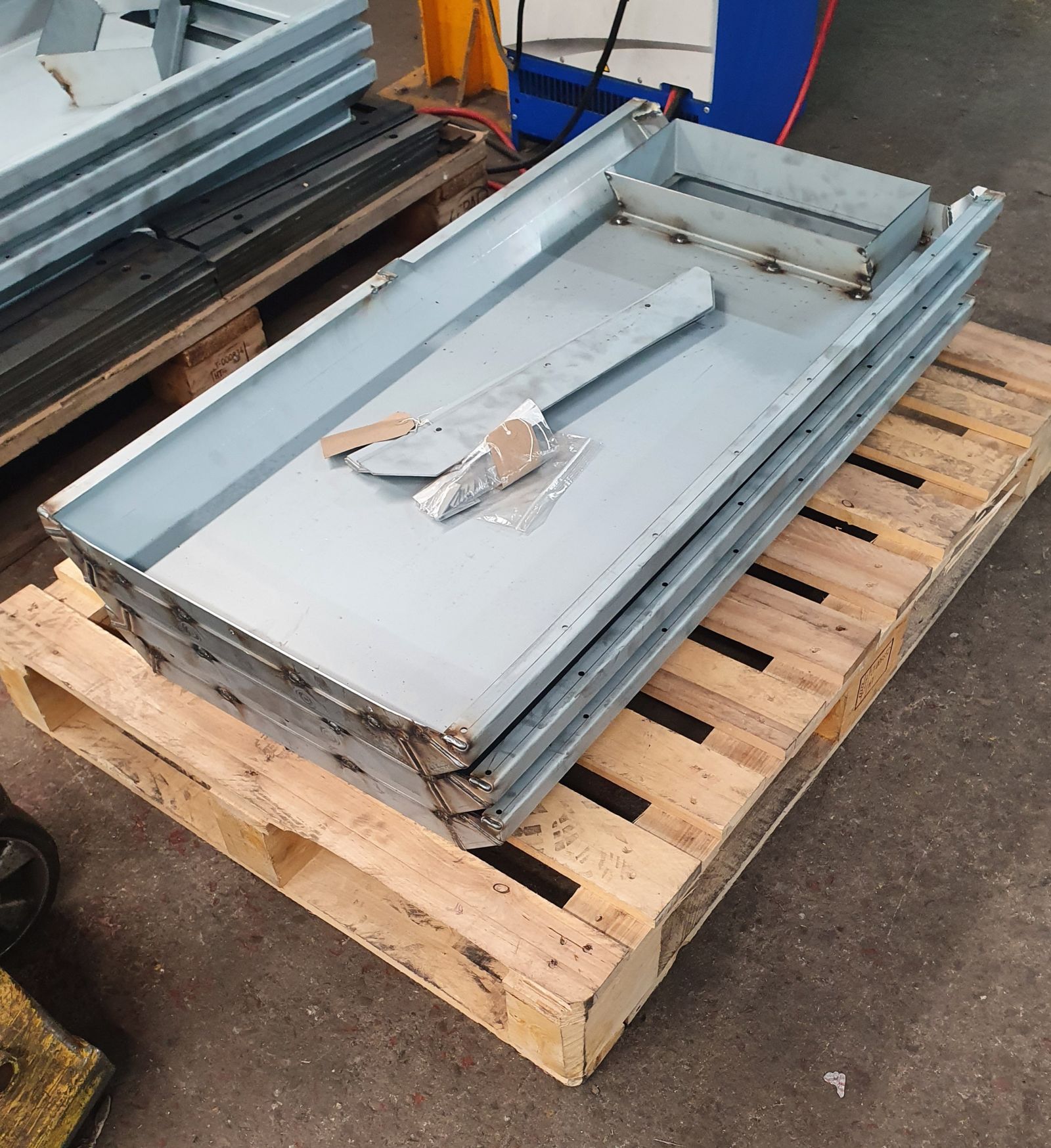
Street furniture for local councils
Litter bins are part of our portfolio. This shot details 2mm Zintec parts that will be fabricated into a litter bin.
The bin door shown, has been bent, assembled and welded, it will be primed ahead of powder coating. The finished units are usually sited on the high street and parks.
Jan 31, 2022
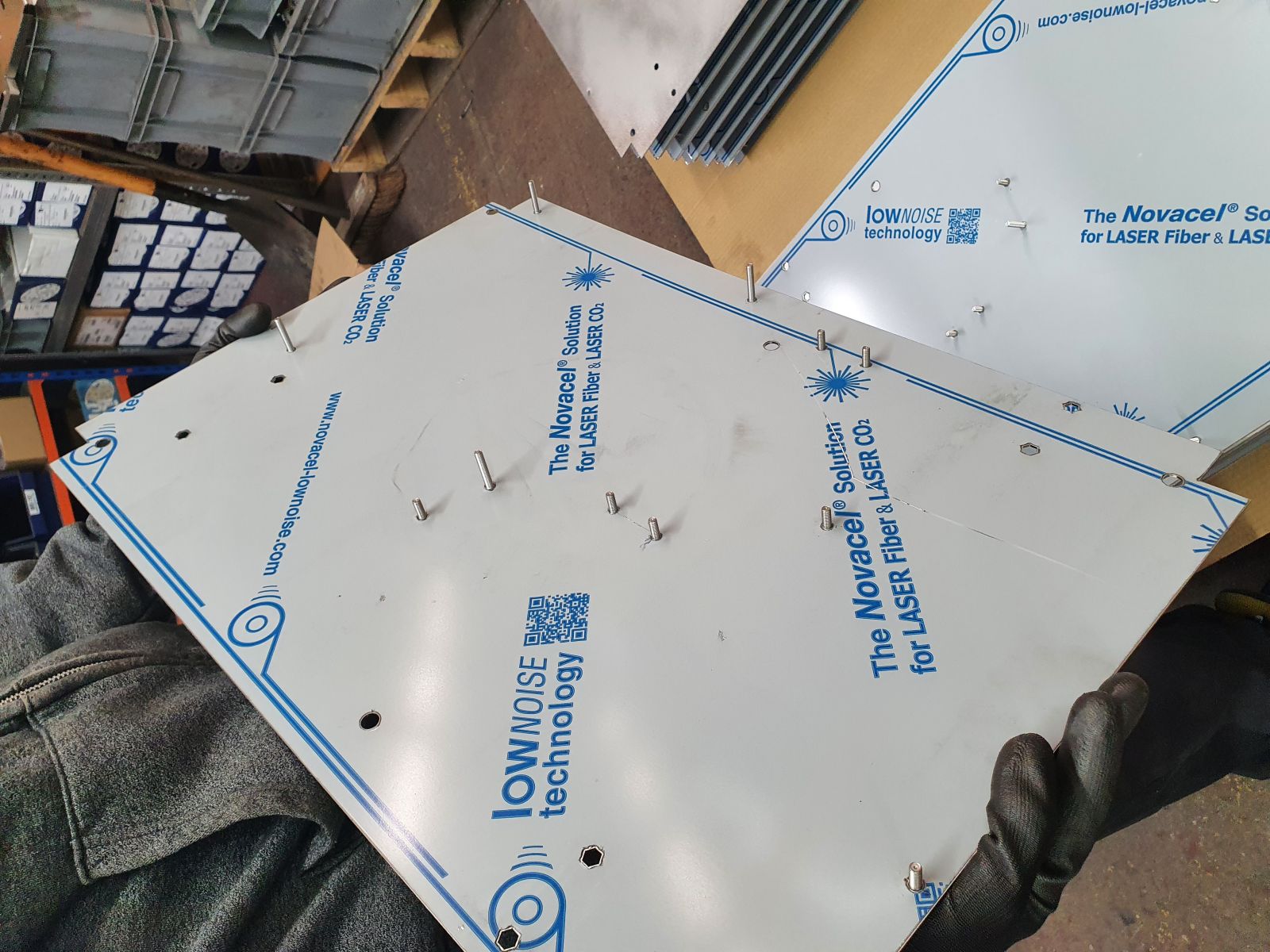
A quality coating for secure laser cutting
These newly laser cut parts are coated in a temporary film to preserve the grained surface finish during inserting.
The coating is secure, meaning nozzle distortion is reduced, ensuring we maintain quality cutting.
Jan 31, 2022
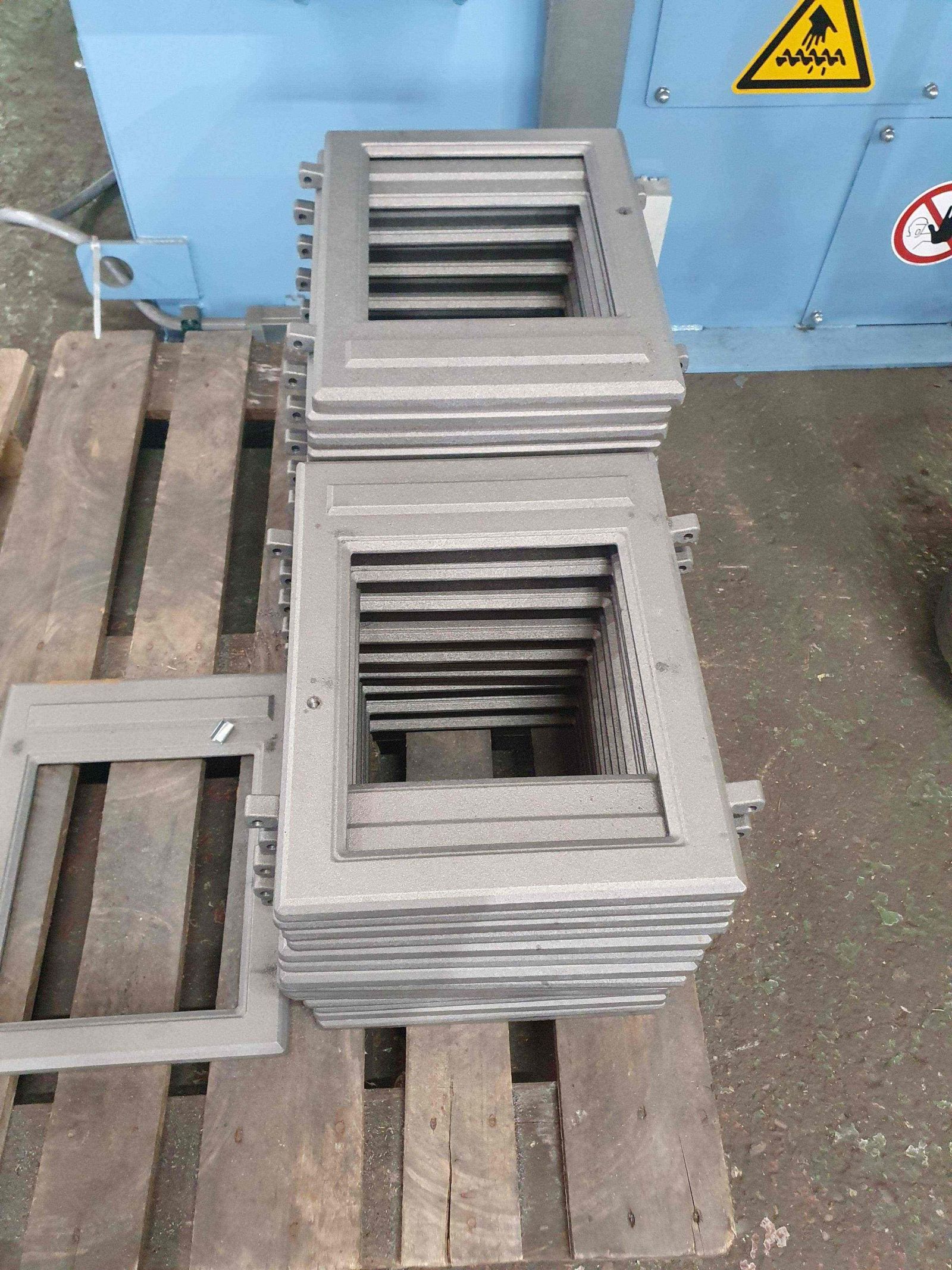
Shot blasting and painting for a long-standing customer
Shown here are the door castings used on the award-winning log burner stoves we produce.
When received from our customer, the doors are drilled and tapped for various fitments, before being prepared to go into our new rotary shot blaster. They are finished with high temperature wet paint.
This is another long-standing customer relationship that we have established over the years and continue to build.
Send an enquiry
Whatever the project, if you’re looking for quality, expert fabrication then we have the team to help.
Stay in the loop
Keep up to date with our latest news and offering by subscribing to our regular newsletter.
No spam ever.