The Production Line
May 22, 2023
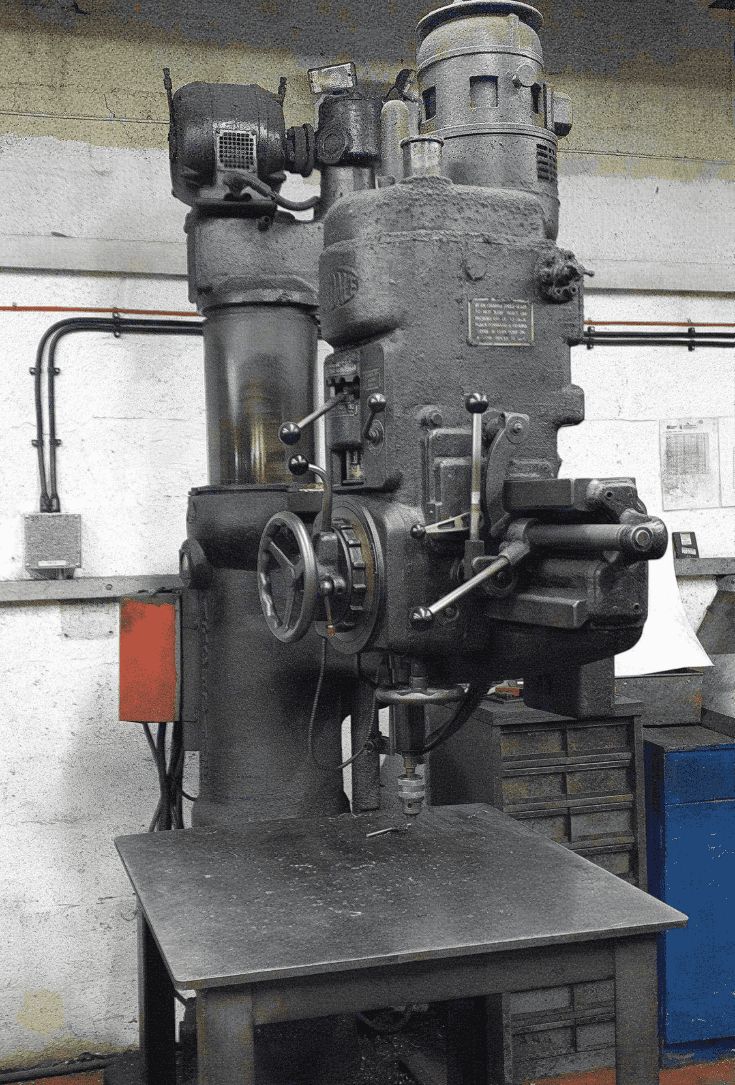
A rich manufacturing history
We're proud to invest in the best possible equipment, as it ensures long-term value for our business. Recently, we were surprised to discover that one of our drills is about 120 years old - a testament to its durability and the dedication of those who have maintained it.
Industrial machinery can have a long lifespan with proper maintenance, and preserving this drill allows us to continue using a reliable and effective tool in our manufacturing process, while also honouring our history.
May 15, 2023
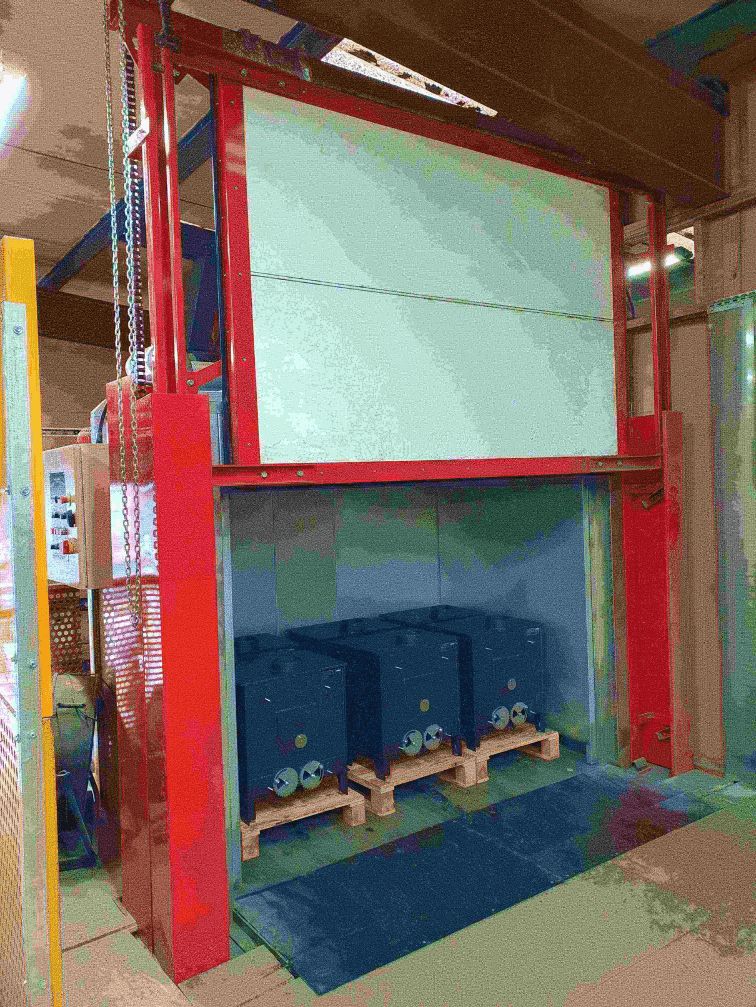
Delivering a quality service requires investment
We've invested in a new industrial curing oven to enhance our operations and improve customer service. Since 2017 we have been producing award-winning stoves for a leading British supplier, and have expanded to manufacture their entire range.
We value our partnership and strive to provide the best service by investing in the latest technology. This oven will create a more durable finish on the steel stoves by evenly distributing and drying the paint. We are also continually acquiring and looking for new technology that will help enhance our service speed and quality.
May 09, 2023
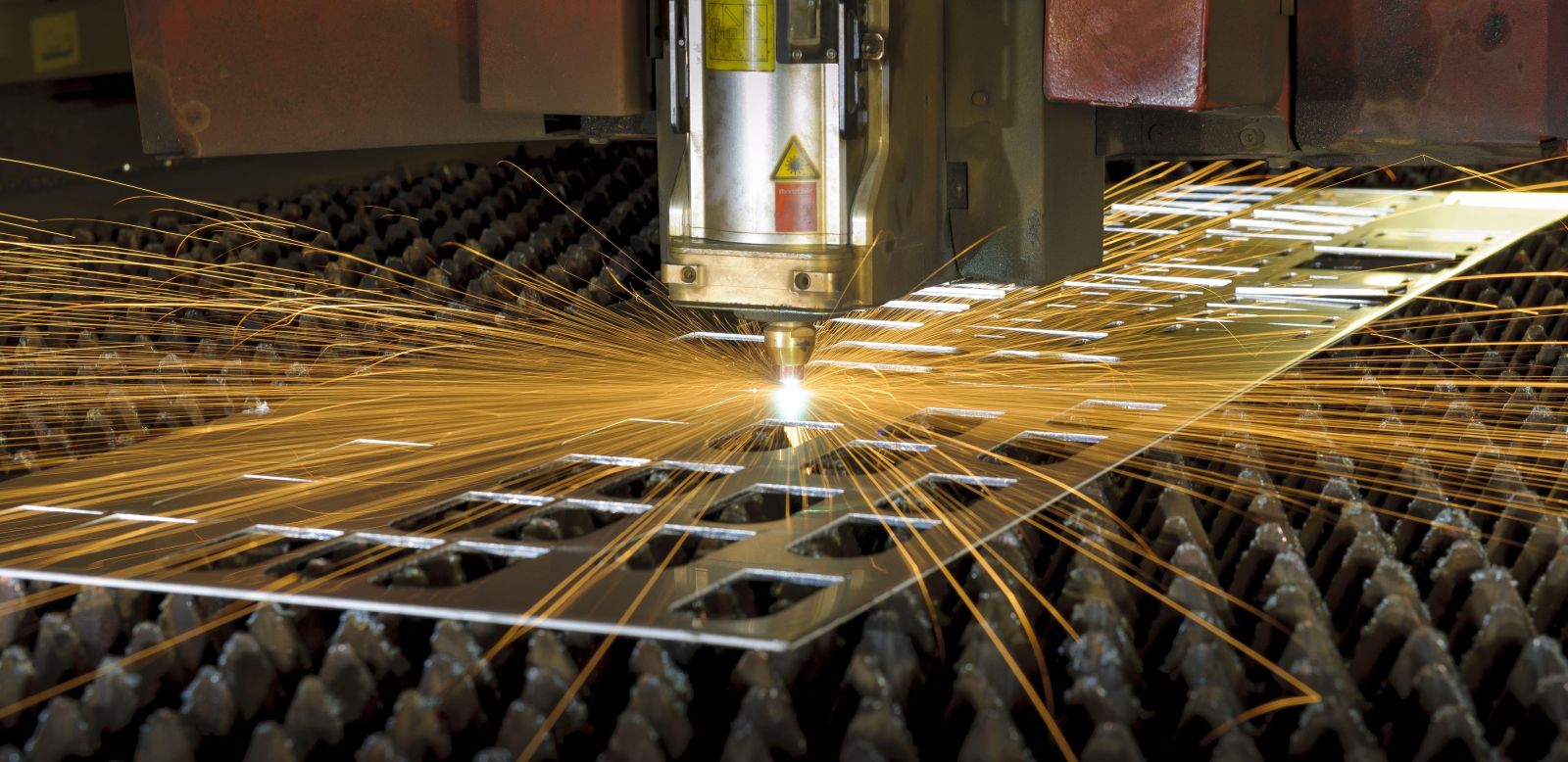
What makes us a leading industrial laser cutting supplier?
As a leading provider of industrial laser cutting and fabrication in Nottingham, we take great pride in developing enduring partnerships with our clients. We supply a diverse number of sectors, including the automation industry, healthcare services, and the military, among others. This has given us vast experience in working with an extensive range of specifications, each with varying levels of intricacy.
Feb 07, 2023
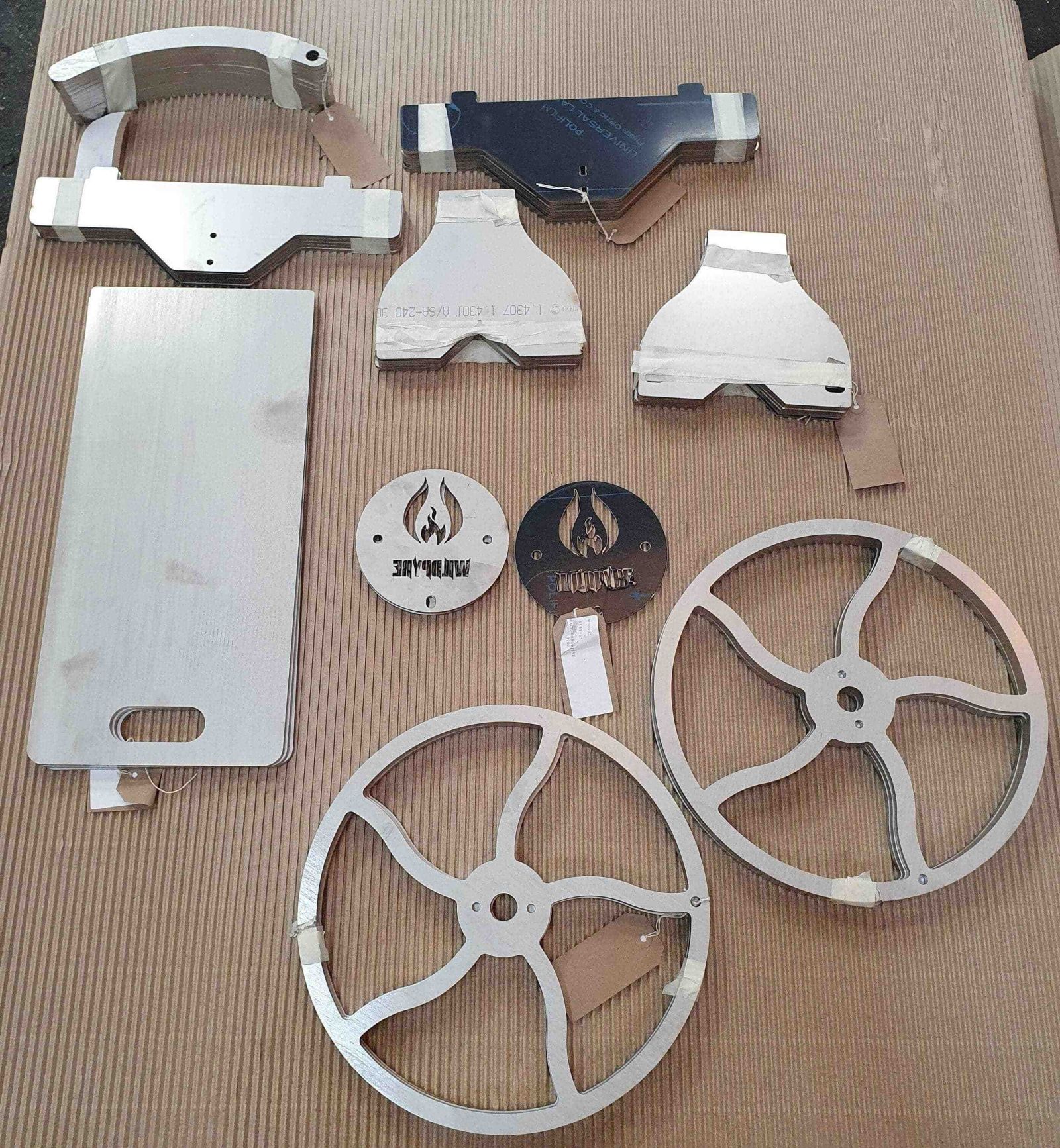
Quality laser cutting for a premium grill supplier
For this project, our customer provides us with drawings, which we laser cut, supplying them with flat kits of parts for them to fabricate in-house. This particular customer manufactures and supplies high-quality steel grills and fire tables for commercial and domestic use.
Jan 18, 2023
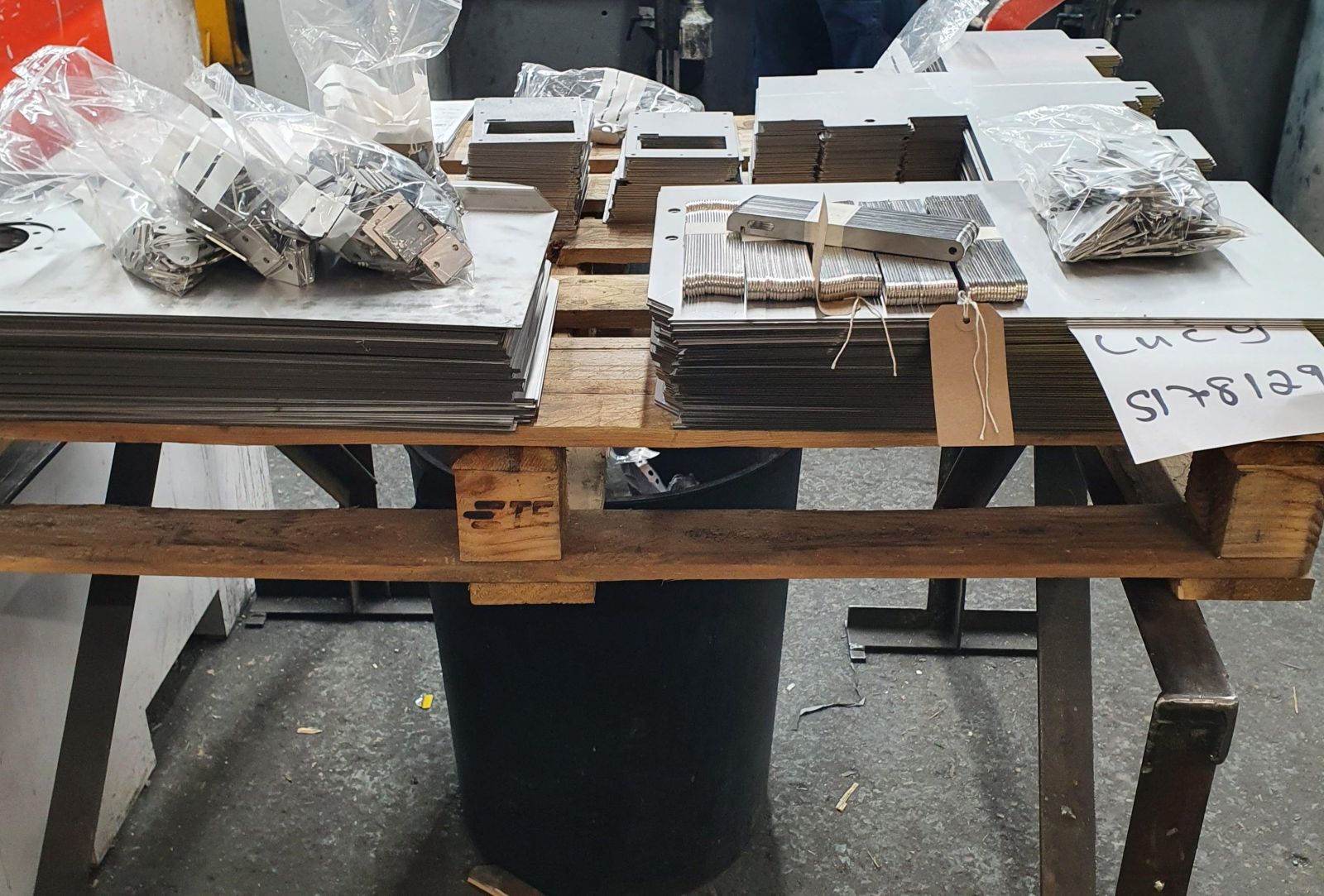
Commercial laser cutting with precision
Precision and cleanliness make industrial laser cutting a popular technique across many of industries, including medical, electrical, structural, automotive, and shop-fitting, as well as speciality sectors like signage, decorative, and water features.
Being specialists, we serve an extremely diverse customer base, and we believe that flexibility is critical to delivering excellent service.
To find out more about the laser-cut components we produce, go to our cutting page.
Aug 15, 2022
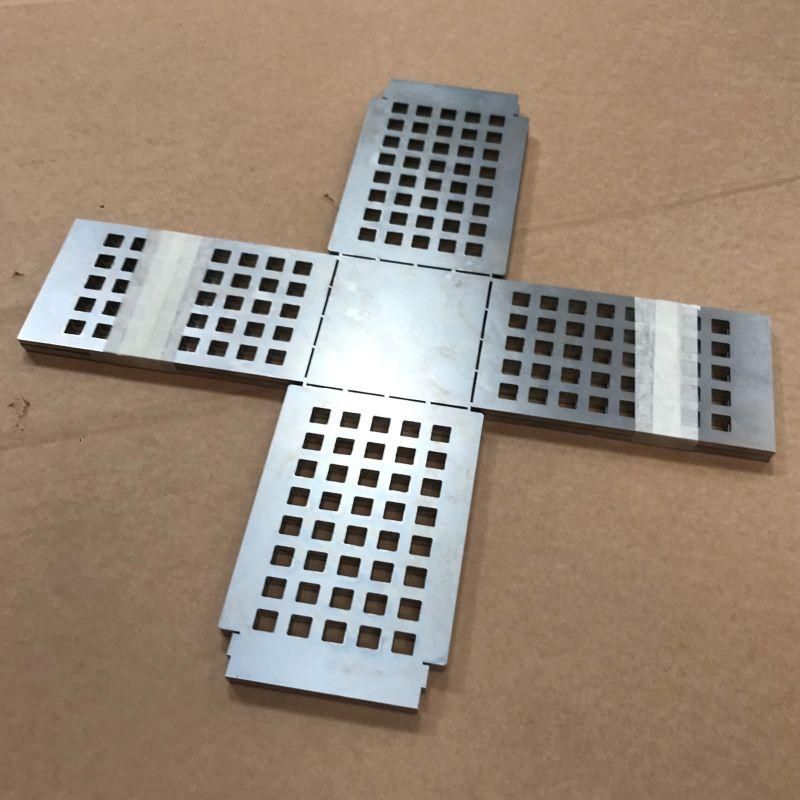
Laser cutting for a range of industries and businesses
We don't just cut items that are going to be "industrial" in their use. Using either our 6 kW, 4 kW or 12 kw Fibre Laser Cutting systems, we often laser cut pieces that our customers turn into everyday objects, such as this condiment basket used in a well-known chicken fast food restaurant chain.
Send an enquiry
Whatever the project, if you’re looking for quality, expert fabrication then we have the team to help.
Stay in the loop
Keep up to date with our latest news and offering by subscribing to our regular newsletter.
No spam ever.